In this Article
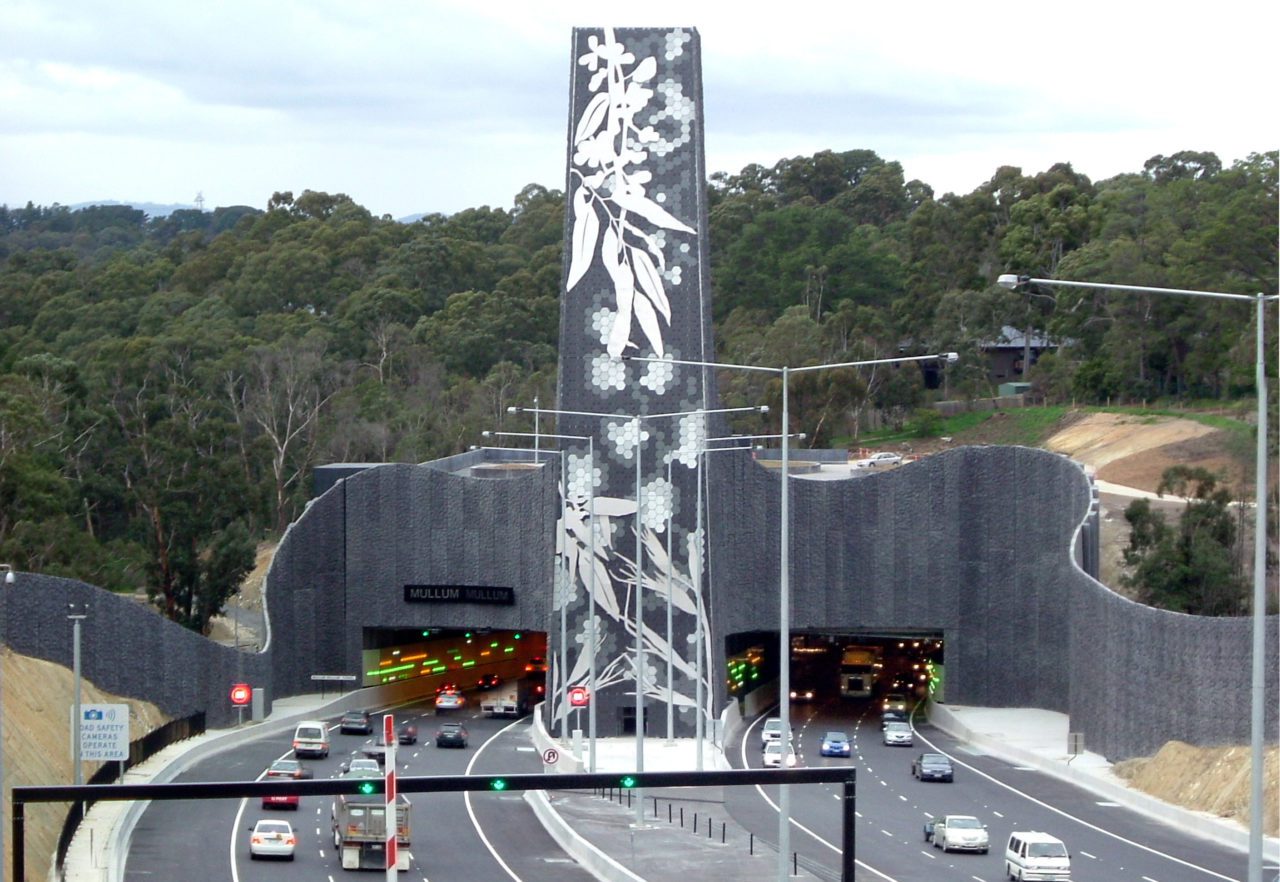
When driving through one of Eastlink’s 1.6-kilometre traffic tunnels, it’s difficult to imagine everything that is going on behind the scenes to keep all those vehicles moving smoothly and safely.
Each tunnel that forms part of this eastern Melbourne arterial has a ventilation plant at its exit and large fans to capture the air and the exhaust fumes it contains. The air is dispersed through 47-metre-high ventilation stacks.
Eastlink is successfully using our AlphaX Machine Health Monitor (MHM) and wireless vibration sensors to measure vibrations in its tunnels.
This Internet of Things (IoT) device measures a tiny 12cm x 9cm x 5.5cm.
It’s designed to be affixed to any machine such as a fan or pump. The customer inserts a battery pack and plugs in various sensors to the ports, turn it on and away it goes. The device starts measuring whatever 60+ available sensors are designed to measuring.
AlphaX transmits the data on one of four networks: the cellular network (the same one that your phone uses), Sigfox and LoRaWAN™, which are low-cost narrow-band networks for securely connecting IoT sensors to the Cloud, and Wi-Fi. Customers can also connect using Bluetooth, but that’s fairly low range and doesn’t go far.
The customer is able to access a live stream of data via the software and an internet connection from anywhere in the world.
The Automated Approach
While it is standard procedure to monitor vibrations in an industrial setting, the AlphaX MHM is a new way of monitoring – an automated way of monitoring.
In most industries a site manager or consultant is required to periodically collect data using a vibration data logger, log in to the software to check and the machines condition manually.
Here at M innovation, we have written artificial intelligence (AI) scripts that actually do the monitoring for the user.
Take the Eastlink fans, for example. The customer receives a live stream of data that updates every hour. With the help of wireless vibration sensors, they are able to actually drill down to a particular jet fan and see an overview of what is happening with that fan. But then they can also drill down to see what is happening with each frequency component of that vibration.
For example, there is component for bearings and another component for rotation because the speed of the fan gives a different frequency to the speed of the bearings. We monitor each of those different frequency to monitor the different components of vibration.
Wireless Vibration Sensors Enable Predictive Analytics
The AlphaX is a powerful tool for proactive maintenance in a variety of industries. The beauty of our system is our AI script looks at those different components and says, ‘the low frequencies are increasing… the fan will be out of balance in 20 days.’ Or ‘The bearing frequencies are increasing, at this rate they will fail in 45 days..’
We are able to automatically detect and trend issues before they become an issue.
We offer auto ISO analysis – auto analysis based on ISO10816 international standards for vibration monitoring. We have our own auto bearing analysis, which has been developed from 20 years of experience. And we can also provide the option for user-defined limits for specialised equipment.
Fewer Experts Required
Currently, site managers need the expertise to manually analyse data or they need to hire consultants to take care of it.
With AlphaX, we are flipping that on its head. You actually don’t need any expertise, the system does the analysis for you. The automated system also removes the need to go on site for data collection purposes so reliability engineers and technicians can get on with solving root causes, not fault finding and diagnostics.
All you need to know is you that have a fault and you need to fix it. And that’s all maintenance teams really care about, right? AlphaX notifies you through automatically generated SMS and email alerts.
Increased Accuracy
The automated system is more accurate than hiring an analyst because it removes human error and bias.
It’s also easier to identify trends because you are able to process raw data continuously. Rather than measuring once a week, the wireless vibration sensors enable you to receive data daily or even hourly. Our software enables you to spot trends that you might otherwise miss or that might take you much longer to notice.
This tool for continual improvement has major cost benefits because small malfunctions can be rectified before they escalate into major issues.
Good Vibrations
Automate your vibration monitoring and optimise your system’s performance with AlphaX and wireless vibration sensors. This low-cost but powerful industrial IoT device provides a proactive maintenance solution for a variety of industries
Related Blog Posts
How Smart Cities Connect: Getting Started with Edge AI and IoT Technology
How to Get Started with Edge AI and IoT Technologies in Smart Cities: Overcoming Integration Challenges In recent years, the concept of smart cities has evolved from a futuristic Read More
5 Step Strategy: Ensuring Security and Privacy in 15-Minute Smart Cities
Introduction Ensuring security and privacy in 15-minute smart cities is a critical challenge as urban areas become increasingly connected through IoT and edge AI technologies. These cities aim to Read More
What is a smart city and the challenge of legacy systems
How to Get Started with Integrating Legacy Systems in Smart Cities Smart cities are transforming urban landscapes by leveraging technology to improve the quality of life for residents. However, Read More